SMC Process
Resin paste, comprised of resin, filler, catalyst and other additives, is precisely applied onto the lower layer of film on a SMC machine, The glass roving is chopped onto the resin paste and covered by another resin film. Thus formed sandwich is pulled through compaction section to form the semi-product¡ªSheet Molding compound.
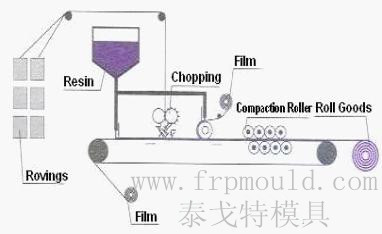
BMC Process
A bulk molding compound is made by combining glass chopped strands, resin, filler, catalyst and other additives. This compound is processed by compression molding or injection molding to form the finished composite parts.
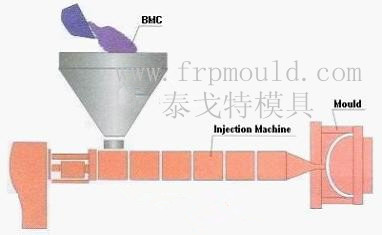
GMT Process
Generally two layer of reinforcing mat are sandwiched between three layers sheet of polypropylene, which is then heated and consolidated into a semi-finished sheet product. The semi-finished sheets are then heated and molded by stamping or compression process to make complex finished parts.
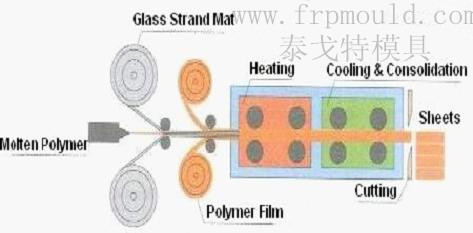
LFT-D
Polymer pellets and glass roving are all introduced into a twin-screw extruder where the polymer is melted and compound is formed. Then the molten compound is directly molded into the final parts by injection or compression molding process. LFT-G The thermoplastic polymer is heated to a molten phase and pumped into the die-head. The continuous roving is pulled through a dispersion die to ensure the fiberglass and polymer and polymer impregrated fully and to get consolidated rods. After cooling, the rod is chopped into reinforced pellets.
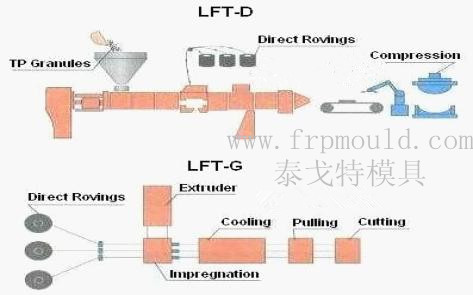
Hand Lay-up Process
The reinforcement, in forms of fiberglass strands, mat or woven roving, is first laid into a mould which has been pre-coated with a release agent and a get coat. Then a resin mix is applied by hand using a brush or spray gun. A roller is then used to ensure uniform impregnation, complete glass wet-out, and removal of any trapped air bubbles. This operation is repeated until the desired thickness of the structure is obtained. After curing at room temperature or under heating condition, the finished parts are formed.
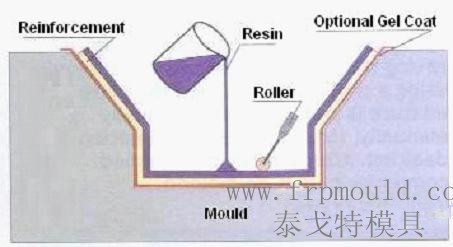
RTM (Resin Transfer Molding) is a low pressure, closed molding process, where a mixed resin and catalyst are injected into a closed mold containing a fiber pack or preform. After the resin has cured, the mold can be opened and the finished component removed. A wide range of resin systems can be used including: polyester, vinylester, epoxy, phenolic and methyl methacrylates, combined with pigments and fillers including aluminum trihydrates and calcium carbonates if required. The fiber pack can be glass, carbon, arimid, or a combination of these.
|